Indice Contenuti
- Perché sono necessari i dispositivi di sicurezza nei sistemi AGV
- Sicurezza e Affidabilità
- Sicurezza del personale addetto all’uso e alla manutenzione
- Sicurezza del personale operante negli stessi spazi di impiego degli AGV
- Gli AGV e gli oggetti circostanti
- Normative per la sicurezza
- Dispositivi di sicurezza
- Dispositivi hardware-based di sicurezza
- Sensori ottici di prossimità
- Paraurti meccanici (Bumper)
- Sensori a contatto (profili sensibili di sicurezza)
- Dispositivi HW per le funzioni operative della macchina
- Pulsanti di arresto di emergenza (e-stop)
- Dispositivi di segnalazione acustica (Buzzer)
- Spie luminose di segnalazione
- Dispositivi HW per le funzioni operative della macchina
- Sensori di rilevamento carico
- Sensori di presenza carico a bordo macchina
- Fine corsa di sicurezza
- Dispositivi di sicurezza software
- Sistemi di sicurezza software a bordo macchina
- Sistemi di sicurezza software all’interno del programma di gestione del traffico AGV
- Dispositivi hardware-based di sicurezza
Perché sono necessari i dispositivi di sicurezza nei sistemi AGV
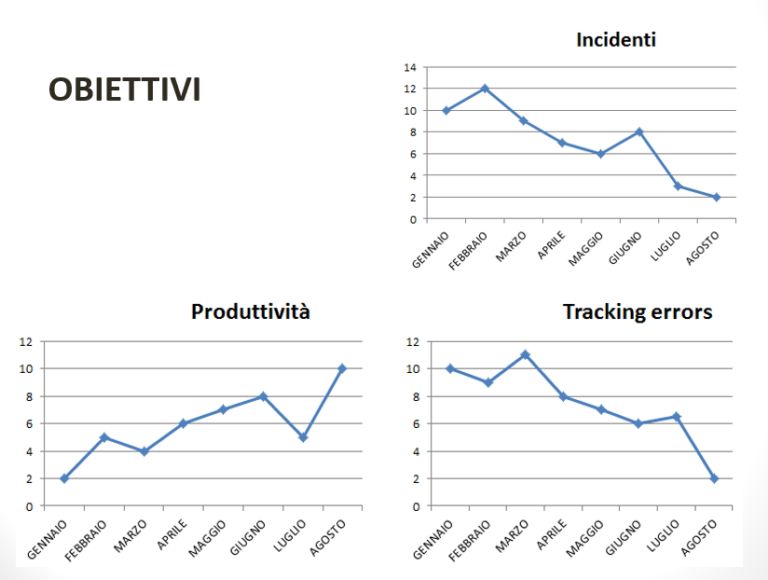
Un sistema AGV è composto da macchine caratterizzate da dimensioni ingombranti e masse elevate che spesso si muovono anche a velocità di crociera abbastanza sostenuta (anche fino a 2 metri al secondo!), creando quindi un rischio concreto per le persone che si dovessero trovare sul loro percorso; spesso si trovano a trasportare carichi anch’essi grandi e pesanti, è necessario quindi che siano sempre provvisti di dispositivi di sicurezza che garantiscano in primo luogo l’incolumità di chi opera intorno agli AGV (safety) e anche l’integrità del carico che stanno trasportando per un fattore di produttività (reliability).
È possibile raggruppare i dispositivi di sicurezza in quattro categorie: Per l’incolumità del personale, del materiale, del processo e del veicolo stesso.
- Personale: distanziatori, bumper e bordi sensibili anti schiacciamento
- Materiali o infrastrutture: fotocellule, sensori a pressione, sensori di presenza.
- Processo: Lettori di codici a barre, lettori RFID.
- Veicolo: bordi sensibili di sicurezza, PLS (Proximity Laser Scanner).
Sicurezza e affidabilità
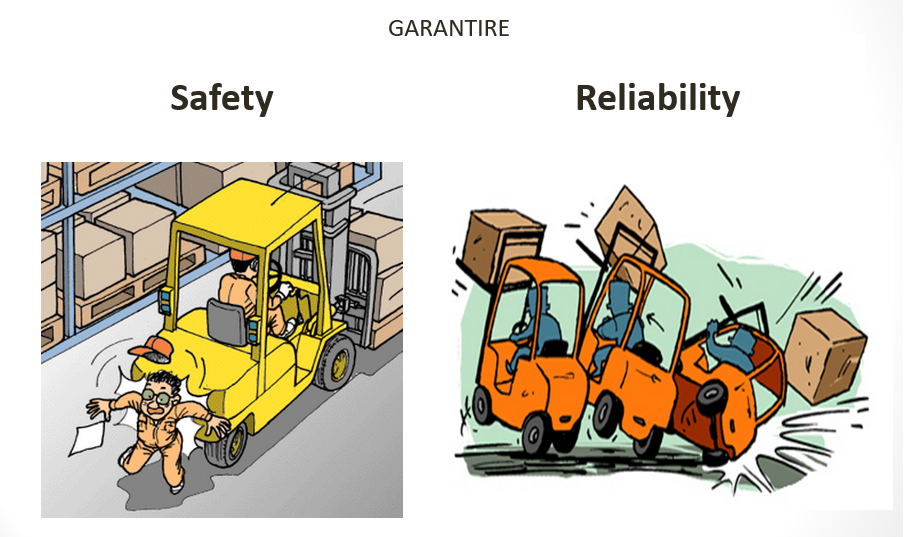
Per un sistema AGV, è in primo luogo, importante che venga garantita la sicurezza del personale che opera negli stessi spazi degli AGV , per esempio operatori o personale di manutenzione, ma una volta che questo requisito è stato considerato soddisfatto, un sistema AGV, per essere ritenuto un buon investimento, deve soddisfare i seguenti requisiti:
- massima produttività, con
- minimo numero di incidenti a persone e cose, e
- nessun errore di tracciabilità dei carichi.
La tracciabilità dei carichi, è indispensabile, per esempio, nelle industrie alimentari e nel farmaceutico, dove il veicolo deve assicurare il prelievo del corretto oggetto. A garantire ciò, a bordo macchina sono montati o lettori di codice a barre o lettori RFID, a secondo se il carico dispone di un codice a barre o di un TAG.
I dispositivi di sicurezza, montati sui veicoli, garantiscono l’ottenimento dei suddetti requisiti, facendo così dei sistemi AGV un ottimo compromesso tra sicurezza, produttività e affidabilità.
Sicurezza del personale addetto all’uso e alla manutenzione
Per quanto riguarda la sicurezza del personale addetto all’uso e alla manutenzione degli AGV, tutto è giostrato da una serie di norme, che generalmente vengono fornite dal produttore dei veicoli insieme ai manuali di manutenzione, o che vengono direttamente insegnate da un tecnico della casa produttrice a chi dovrà lavorare a diretto contatto con gli AGV grazie ad un certo numero di ore di training.
La stretta osservanza di queste norme, che possono essere ad esempio la corretta sequenza di azioni da seguire per poter sostituire una batteria o di un altro componente che possa rivelarsi pericoloso o le istruzioni per utilizzare in sicurezza la guida manuale quando necessario, garantisce la sicurezza di chi opera con gli AGV.
Sicurezza del personale operante negli stessi spazi di impiego degli AGV
I metodi di sicurezza nei sistemi AGV più utilizzati sono dispositivi che permettono alla macchina di rilevare presenze estranee sul suo percorso in modo tale da potersi fermare tempestivamente, e sistemi che permettano alla macchina di trasportare il carico da una stazione all’altra preservandone l’integrità.
I dispositivi più utilizzati sono sensori fisici che tramite pressione o tramite scansione rilevano un possibile rischio che viene tempestivamente segnalato all’AGV, che provvede alla frenata. Ad esempio se durante la normale operatività di un AGV qualcuno dovesse passare davanti alla macchina in movimento a una distanza ritenuta pericolosa (generalmente a 1 o 2 metri se si tratta di scanner o 1 metro se si tratta di un bumper di sicurezza) l’AGV dovrà fermarsi immanente per evitare lo scontro. Inoltre spesso sono provvisti di un profilo di sicurezza sensibile che in caso di contatto in ogni punto del contorno della macchina invia un segnale d’allarme che attiva la frenata o comunque il rallentamento.
Inoltre sono spesso provvisti di pulsanti di arresto rapido di emergenza in più di un punto sul telaio della macchina in modo che in caso di pericolo o di necessità possano essere premuti da un operatore; l’AGV anche in questo caso provvederà a una veloce frenata indipendentemente dal task che sta svolgendo. Il pulsante rimarrà premuto fino allo sblocco manuale dello stesso, e l’AGV rimarrà fermo di conseguenza.
Un altro metodo per garantire la sicurezza sono segnali acustici e visivi che l’AGV produce durante le sue manovre per far si che la sua presenza possa essere rilevata da chiunque stia operando nei dintorni.
Gli AGV e gli oggetti circostanti
I dispositivi che permettono all’AGV di salvaguardare la sicurezza di chi opera nei suoi stessi spazi, permettono anche di garantire l’integrità degli oggetti che compongono lo scenario in cui esso si muove.
Ad esempio uno scanner laser permetterà all’AGV sia di evitare di scontrarsi contro una persona che contro un oggetto fisico che si dovesse trovare sul suo percorso, in modo da prevenire un danneggiamento anche critico su entrambi.
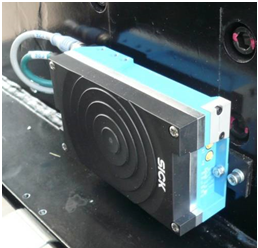
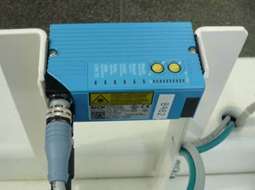
Esistono però ulteriori dispositivi che garantiscono questo tipo di sicurezza che però sono hanno questo come unico compito, ma generalmente sono dispositivi software, poiché sono caratteristiche intrinseche nel del software di gestione del sistema che impediscono alla macchina di uscire dal suo percorso e di danneggiare quindi cose che non dovrebbero mai entrare in comunicazione con i compiti del veicolo.
Normative per la sicurezza
Generalmente i veicoli vengono costruiti in conformità a quanto applicabile delle seguenti normative che trattano, da diversi punti di vista, aspetti relativi alla sicurezza:
Ulteriori norme e standard seguiti sono:
- EN1525, Safety of industrial trucks – Driverless trucks and their systems.
- SS-EN 60504-1 Safety of machinery.
- Analisi dei rischi secondo la direttiva 2006/42/EC.
Le seguenti raccomandazioni andrebbero comunque seguite nei sistemi AGV:
- I percorsi degli AGV dovrebbero essere chiaramente contrassegnati, incluse le zone in cui l’AGV dovrà curvare.
- Gli operai dovrebbero essere addestrati su come fare attenzione agli AGV e a come tenersi fuori dal percorso degli AGV in caso uno di essi sia in arrivo.
Dei coni di sicurezza dovrebbero essere accuratamente disposti intorno ad un’area di lavoro quando si opera su o vicino ad un percorso AGV.
Dispositivi di sicurezza
Esistono fondamentalmente due famiglie di dispositivi di sicurezza, i dispositivi basati su hardware dedicato (indicati con hardware-based per brevità) e i dispositivi interamente software, che come vedremo sono più dedicati a compiti di affidabilità, piuttosto che di sicurezza in senso stretto.
La più ricca categoria di dispositivi di sicurezza è quella dei dispositivi hardware-based, ovvero sensori fisici che interagiscono direttamente con l’ambiente circostante rilevando ostacoli e persone che interferiscano con la traiettoria di movimento dell’AGV o con il carico che esso trasporta, e che comunicano direttamente con delle schede montate a bordo macchina che gestiscono i veri segnali in modo diverso, ad esempio ordinando alla macchina di rallentare, di fermarsi o cambiando la frequenza d’intermittenza delle spie luminose, a seconda delle esigenze.
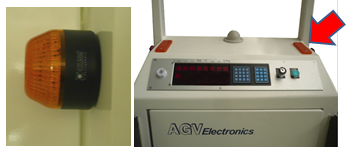
I dispositivi che agiscono via software invece si occupano di un diverso tipo di sicurezza, che in senso normativo non è sicurezza ma affidabilità, e garantiscono principalmente quindi una buona reliability del sistema; ad esempio si occupano di gestire la comunicazione tra l’AGV e le stazioni in modo tale da poter coordinare correttamente il carico e lo scarico del prodotto trasportato, oppure si occupano di fare in modo che gli AGV non vadano mai in collisione tra di loro gestendo le traiettorie e i percorsi in modo dinamico.
Dispositivi hardware-based di sicurezza
Nelle seguenti immagini sono mostrati alcuni esempi di dispositivi di sicurezza hardware-based:
Sensori ottici di prossimità
I principali dispositivi sono sensori di prossimità, ovvero sensori che rilevano la presenza di qualcuno o qualcosa a una certa distanza dal veicolo stesso, ad esempio a uno o due metri di distanza. I sensori inviano un segnale alla scheda che gestisce i segnali, che di conseguenza agisce sugli azionamenti del veicolo.
Sono disposti generalmente sulla parte frontale dell’AGV, quindi diretti nella direzione del senso di marcia, ma non mancano i casi in cui sono disposti anche sul retro in modo da avere una scansione di un’area vasta intorno al veicolo per una maggiore sicurezza.
I sensori di questo tipo più utilizzati sono scanner laser che continuano a scannerizzare l’area durante tutto il periodo di operatività dell’AGV fino ad una distanza che può essere decisa via software. Generalmente sono previsti due livelli di controllo, il primo dei quali fa rallentare l’AGV e in caso il segnale d’allarme persistesse fino all’area del secondo livello, più vicina al veicolo, l’AGV si fermerà del tutto prima di entrare in contatto con l’ostacolo.
Ognuno dei due livelli di controllo accende di conseguenza rispettivamente un led di deverso colore che segnala anche visivamente che un allerta è in corso su di un display presente sul corpo del dispositivo.
Finché l’ostacolo si continuerà a trovare nell’area di controllo l’AGV rimarrà in fase d’arresto (o di rallentamento seguito da un arresto), fino a che l’ostacolo non sarà rimosso, dopo di che il veicolo riprenderà la normale operatività.
Gli scanner laser sono dispositivi ottici quindi è buona norma maneggiarli con cura per evitare un danneggiamento e precluderne il funzionamento, nonostante siano stati progettati per condizioni industriali anche pesanti.
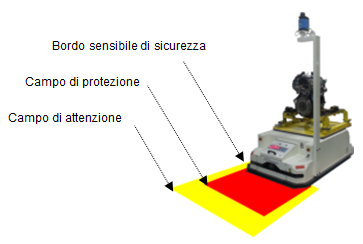
Paraurti meccanici (Bumper)
I paraurti meccanici o bumper, sono sensori a pressione molto sensibili che rilevano il contatto con un oggetto che si venga a trovare nella traiettoria di marcia dell’AGV e generalmente sono sostituiti o vanno in ausilio ai bumper ottici (scanner laser). Possono essere usati in ausilio ai bumper laser in caso questi ultimi, per una qualunque ragione, non stiano funzionando correttamente o il loro raggio d’azione non sia abbastanza coprente nelle zone molto vicine al veicolo.
Vengono normalmente montati sulla parte del veicolo frontale rispetto al senso di marcia, quindi, nel caso il veicolo sia bidirezionale, possono essere montati sia frontalmente che sulla parte posteriore.
Due delle possibili modalità di funzionamento sono:
- A fotocellule – sono presenti dentro il bumper due riflettori che comunicano con le due fotocellule sul veicolo di fronte ad essi, quando il bumper viene premuto in seguito al contatto con un ostacolo, il segnale tra fotocellula e riflettore si interrompe, viene di seguito inviato un segnale alla scheda di controllo del veicolo che ordina all’AGV di fermarsi immediatamente.
- A micro-switch – due cordicelle tese tengono i micro-switch disattivati. Quando il bumper viene premuto, le cordicelle si allentano ed i micro-switch vengono attivati
Una volta attivato il bumper, l’AGV resterà bloccato fino a che il bumper non tornerà in condizione di riposo e quindi si sia ripristinata la comunicazione tra fotocellula e sensore, o cordicelle e micro-switch.
Tensione delle cordicelle o fotocellule possono essere tarate per aumentarne o diminuirne la sensibilità del bumper, e questa procedura è buona norma che venga effettuata con cura.
Su alcuni dispositivi è presente anche un ingresso di test per verificarne il corretto funzionamento e quindi garantire la sicurezza durante le operazioni.
Sensori a contatto (profili sensibili di sicurezza)
L’AGV può essere provvisto di profili sensibili di di sicurezza su tutti e quattro i lati o in alcuni casi solo sui due lati.
Sono profili in gomma montati su profilati di alluminio e seguono tutto il bordo del veicolo nel punto in cui è più probabile che un eventuale corpo estraneo venga a contatto con la macchina. All’interno dei profili in gomma vi sono fili rame collegati a una centralina, a cui manda un eventuale segnale di avvenuta pressione.
L’unità genererà, quando viene compressa, un arresto dell’AGV e quest’ultimo rimarrà fermo finché perdurerà la pressione.
Lo scopo dei bordi sensibili è quello di proteggere il veicolo, quindi possono essere categorizzati tra i dispositivi che servono a mantenere una buona reliability della macchina oltre che per un fattore di safety.
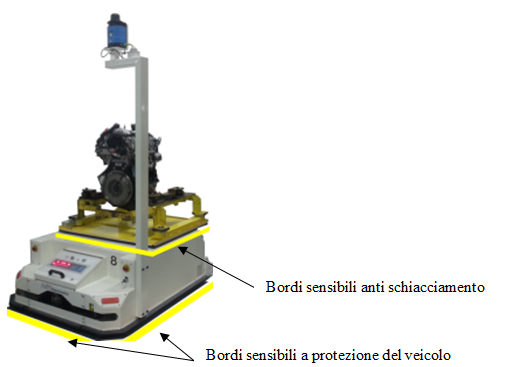
Pulsanti di arresto di emergenza (e-stop)
I pulsanti di emergenza (o e-stop) sono dispositivi di sicurezza che servono a fermare l’AGV quando non è possibile farlo con metodi tradizionali, non è gestito via software ma è direttamene connesso con il circuito di sicurezza hardware-based. Sono caratterizzati da un aspetto di facile riconoscimento, in modo tale che chiunque possa usufruirne in caso di emergenza.
Gli AGV sono sempre provvisti di uno o più pulsanti di emergenza, che possono essere premuti per bypassare ogni dispositivo di sicurezza presente sulla macchina in caso di emergenza o in caso l’AGV non abbia risposto correttamente a un input di emergenza.
Istantaneamente dopo aver premuto il pulsante di emergenza l’AGV si ferma istantaneamente interrompendo qualsiasi operazione stia svolgendo. Spesso la fermata si accompagna con un LED luminoso che ne segnala la fermata di emergenza e talvolta con un segnale acustico.
L’AGV dovrebbe a questo punto restare fermo fino a che l’emergenza non si è estinta e quindi fino a che il pulsante non venga premuto nuovamente. Spesso i pulsanti sono ad incastro e devono essere svitati di un certo angolo per essere estratti e in altri casi è necessaria una chiave per poter sbloccare il tasto, in modo che la condizione di emergenza permanga sino a che non sia un operatore a decidere che l’AGV possa prendere la sua normale operatività.
Generalmente al pulsante di emergenza si associa un pulsante di restart, che è necessario premere dopo aver rilasciato l’e-stop per poter riprendere le operazioni.

Dispositivi di segnalazione acustica (Buzzer)
Gli AGV spesso dispongono di un dispositivo di segnalazione acustica, generalmente chiamato buzzer, o cicalino, che può produrre diversi suoni in base alle diverse situazioni che si presentano.
Ad esempio può produrre una determinata sequenza di suoni quando il veicolo si sta muovendo in retromarcia e una diversa quando sta effettuando una curva.
Lo scopo principale di questo dispositivo è quello di rendere noto a chi si trova nelle vicinanze che l’AGV sta effettuando, o sta per effettuare, una manovra che potrebbe rivelarsi pericolosa, oppure per avvertire gli operatori che si è verificato un evento, come un guasto, un errore o un emergenza, in modo tale che l’AGV possa essere raggiunto tempestivamente.
Alcuni AGV dispongono anche di un lettore mp3 che può avvertire quindi anche vocalmente.
La norma di sicurezza impone che il buzzer emetta una sequenza di suoni ogni volta che l’AGV sta per partire (generalmente 3 secondi prima), in modo che chi si trova nelle vicinanze sappia che il veicolo sta per mettersi in movimento.
Spie luminose di segnalazione
Sui quattro angoli dei veicoli AGV generalmente vengono montate quattro spie luminose, ben visibili da chi opera intorno alla macchina, che servono a segnalare diverse condizioni.
Normalmente le quattro spie lampeggiano con una certa frequenza durante la marcia in modalità automatica dell’AGV.
Quando si presenta un’emergenza, l’AGV si sta muovendo in retromarcia, sta attuando una curva, sta ruotando su se stesso o sta prelevando/scaricando ad una stazione, le spie lampeggiano con frequenza maggiore.
Quando l’AGV è fermo ed inattivo generalmente saranno spente.
Sono dispositivi di sicurezza importanti perché permettono a chiunque di capire immediatamente che tipo di operazione sta svolgendo l’AGV e gli garantiscono anche una buona visibilità anche a distanza elevata in modo tale da spostarsi in tempo dal suo percorso, ed evitare anche quindi rallentamenti o soste inutili che andrebbero ad intaccare la quota produttiva.
Dispositivi HW per le funzioni operative della macchina
La garanzia della correttezza delle funzioni di prelievo, movimento e deposito da e verso le stazioni è gestita tramite fotocellule di rilevamento carico su stazione, sensori per il rilevamento di carico a bordo (flap), sensori di carico sporgente. Anche questa gestione, orientata all’incremento della produttività/affidabilità del sistema, viene spesso indicata come “sicurezza” anche se non riguarda in senso stretto la garanzia di non pericolosità per le persone.
Sensori di rilevamento carico
Sensori di rilevamento carico a bordo stazione: normalmente si tratta di una fotocellula o di un sensore ad ultrasuoni che, installato sull’AGV, determina se a bordo stazione sono presenti dei carichi. Sono dispositivi che aumentano produttività e affidabilità del sistema e non la sicurezza in senso stretto.
Sensori per il controllo di eccedenza carico a bordo macchina: Installati sui lati del veicolo questi sensori comunicano alla centralina dell’AGV se il carico a bordo è in posizione corretta.
Se il veicolo si muovesse con il carico fuoriuscente lateralmente, si potrebbero provocare incidenti lungo il percorso.
Sensori di presenza carico a bordo macchina
Sono sensori utilizzati dalla centralina dell’AGV per determinare la posizione del carico a bordo macchina è piena o vuota, cosi da avere controllo sul carico durante il percorso e nelle fasi di carico / scarico. Anche qui si mira ad aumentare produttività e affidabilità.
Fine corsa di sicurezza
I sensori di sinistra e di destra in posizioni esterne, limitano la corsa della forca telescopica in estensione. Il sensore deve essere regolato in modo la forca telescopica raggiunge l’apertura massima di corsa a destra del veicolo o bordo laterale sinistro. Quando il proximity è attivato, dà un segnale alla scheda di controllo AGV. La sicurezza anche qui è intesa in senso lato poiché anche questo dispositivo migliora affidabilità e produttività del sistema.
Sensori di prossimità
Il sistema è costituito da una coppia di fotocellule, una a bordo machina ed una sulla stazione. Con l’avvicinamento del veicolo, la fotocellula a bordo macchina, intercetta il raggio ottico emesso dalla fotocellula montata sulla stazione di prelievo/deposito.
Se, durante tutta la fase di carico/scarico (avvicinamento / carico/scarico /allontanamento), la fotocellula a bordo stazione viene spenta, l’AGV blocca ogni attività ed attende la riaccensione della fotocellula.
Non appena la fotocellula montata sulla stazione riprende l’emissione, il veicolo riprende le proprie attività.
La fotocellula montata a bordo stazione è collegata alle sicurezze della stazione, quindi, per riattivare tale fotocellula bisogna, normalmente, ripristinare le anomalie sulla stazione.
Anche qui si ha un incremento dell’indice di affidabilità e produttività e la sicurezza è intesa in senso lato poiché non servono in modo diretto per salvaguardare l’incolumità delle persone.
Dispositivi di sicurezza software
Sistemi di sicurezza software a bordo macchina
- Handshake con stazioni di carico e scarico automatiche. È necessario per sincronizzare lo stato del PLC di controllo della stazione con il processo di carico / scarico dell’oggetto da e verso l’AGV. Se la stazione non è pronta al carico/scarico per motivi di sincronizzazione o barriere di sicurezza off, l’Handshake fallisce e non è possibile effettuare lo scambio carico tra AGV e stazione.
- Attivazione contatti per ricarica batterie. I contatti per la ricarica delle batterie vengono attivati (alimentati) soltanto quando il veicolo si trova esattamente al punto di ricarica. In tal modo si evita di tenere i contatti sempre alimentati. I carica batterie erogano tensione soltanto se rilevano sui contatti una carica superiore ad un determinato voltaggio.
Sistemi di sicurezza software all’interno del programma di gestione del traffico AGV
- Bloccaggio veicoli agli incroci – Il layout è mappato come un grafo pesato di nodi e segmenti. Tramite i nodi è possibile coordinare e sincronizzare i veicoli in modo che non collidano su incroci e curve, oppure nel caso un AGV debba fare retromarcia.
- Bloccaggio SW del veicolo(segnali digitali legati a blocchi SW – se il segnale è a 0 il sistema di controllo ferma il veicolo, quando il segnale diventa 1 il veicolo può continuare il suo percorso)
- Apertura porte: segnali digitali che controllano lo stato di apertura/chiusura delle porte, e segnali digitali che ne attivano la chiusura/apertura. Se il veicolo deve passare il sistema apre la porta, al passaggio del veicolo la porta viene chiusa.
Anche in questo caso ne gergo comunque all’ambito degli AGV vengono indicati come sistemi di sicurezza, ma la sicurezza che portano è intesa in senso lato, poiché lo scopo principale è quello di massimizzare la produttività e l’affidabilità del sistema, e di conseguenza aumenta anche l’indice di safety del sistema.